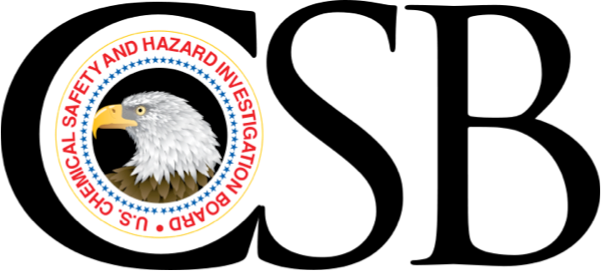
The U.S. Chemical Safety Board (CSB) is responsible for conducting investigation into chemical accidents at industrial facilities. Recently, CSB published the final report about the 2013 Williams Olefins chemical plant explosion case study. CSB summarized the background information on the incident, gave a technical analysis, discussed ways to improve, and provided recommendations.
On June 13, 2013, a fatal explosion occurred at the Williams Olefins Plant in Geismar, Louisiana. Two workers were reported dead and 167 workers reported injuries. The Williams Olefins Plant had a “reboiler”, a heat exchanger that supplies heat to a distillation column, which failed. This reboiler was one of the two that provided heat to the propylene fractionator, that is responsible for separating propylene and propane that the facility produces for the petrochemical industry. The problem arose when the second reboiler was put online after being out of commission for sixteen months. The idle reboiler was assumed to be clean and ready for use, however the plant operators were unaware that the reboiler contained hydrocarbons and its pressure relief system was not operating correctly. When the idle reboiler was put on line, the hydrocarbons it contained began to expand with the rising heat, which created a large pressure increase inside the unit and eventually the container was punctured, which led to a release and subsequent explosion.
The idle reboiler was not properly checked for overpressure protection before being put online. This finding by the CSB pointed to a deficient process safety management program at the facility, especially in enforcing Management of Change (MOC), Pre-Startup Safety Review (PSSR), and Process Hazard Analysis (PHA) programs. Process safety management is an OSHA regulated and required program for facilities that manage highly hazardous chemicals. MOC failed in this instance because it was intended to be completed prior to installing new equipment, but in this case the facility did not perform the MOC until after the new valves were installed on the reboilers and at this point serious overpressure hazardous were missed. Since the MOC did not prompt a need for overpressure protection, PHA was not required. If the overpressure hazard was found, a PHA could have identified and controlled that hazard. The PSSR was incorrectly conducted and key process safety questions were overlooked or incorrectly answered, that dealt with conducting a PHA, operating procedures, and checks on pressure relief valves.
The Williams Olefins plant in Geismar did make significant changes follow the incident. They redesigned the reboilers to include pressure relief valves on both sides. The MOC reviews were improved by performing them in a group setting, instead being completed them individually and passed it off to the next person, which can improve hazard identification. The facility also enforces that an MOC needs an approval before any work can begin.
For more information about the Williams Olefins chemical plant explosion, visit: http://www.csb.gov/williams-olefins-plant-explosion-and-fire-/
For more information about Process Safety Management Programs, contact Brian Long or Maria Maciejewski from our Baron Environmental team.